OOF: Finite Element Analysis of Microstructures




Next: Plane Stress and Plane Up: The Element Types Previous: Coordinate Conventions   Contents
Background Material: Basic Anisotropic Thermoelasticity
In the current version of OOF, all elements are triangles consisting of three nodes located at the triangle vertices. The nodes may be located at the boundary of the mesh, or they can be shared with other elements. The elements share information with each other (i.e., how much the corners have been displaced) through their nodes.
The current version of OOF is thermoelastic, and so the pertinent
field quantities are the displacement (vector) field and the
uniform temperature change
. The displacement field imparts
a strain (tensor) field through the rotation-invariant values of
spatial derivatives of the displacement field:
-which is a long-winded way of saying
the nodal displacements impose a strain,
, on the
elements through a predictable formula.
The temperature is given as a difference . This difference
is relative to the temperature at which the initial mesh is stress
free. Each element undergoes a uniform strain,
, in the stress free state (i.e., if the nodes
are completely unrestrained or the stress tensor
). The second rank tensor
is the (symmetric) thermal
expansion tensor. It has additional symmetries according to the point
group of the underlying material. See Nye [2] for a lucid
discussion of how material symmetry is expressed in tensors
representing linear constitutive behavior.
The stress is a second rank tensor which represents the
the total force transmitted in the
-direction through
a planar region with its normal parallel to the
-direction in the limit that the area of the region
shrinks to a point. Torque balance requires that
in linear elasticity.
In linear elasticity, the stress is related to the strains implied by
the displacement field and the stress-free strain4.1
through the linear relation:

The fourth-rank tensor



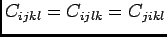
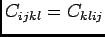
It is convenient to take advantage of the symmetries to represent the
stiffness tensor as a symmetric matrix. This can lead to
silly mistakes since the matrix does not rotate in the usual
straight-forward way. Fortunately, OOF handles the rotations for
you (see Section 4.3). To convert the fourth-rank
tensor into a two dimensional matrix, we adopt the convention in Nye
[2] and replace the six distinct pairs
with a single
integer as follows:
Four Index Tensor Indices ![]() |
11 | 22 | 33 | 23 or 32 | 31 or 13 | 12 or 21 |
Two Index Matrix Indices ![]() |
1 | 2 | 3 | 4 | 5 | 6 |





In OOF, the stiffness components are entered using the matrix notation. The symmetry of each particular material places additional constraints on the stiffness matrices. These additional symmetries are illustrated in Figures 4.2, 4.3, 4.4, and 4.5 (following Nye [2]).




Next: Plane Stress and Plane Up: The Element Types Previous: Coordinate Conventions   Contents /* Send mail to the OOF Team *//* Go to the OOF Home Page */