

Next:Solidification
and coolingUp:MODEL
RESULTSPrevious:MODEL
RESULTS
Capillary forces
Figure 2
shows the dimensionless capillary force on a perfectly rigid fiber parallel
to the substrate as a function of fiber position for a set of dimensionless
parameters given in the top section of table I.
Dimensionless force given in that figure would be multiplied by
to give the true force. These calculations show that for this pad geometry
and parameter set, the horizontal ``aligning'' component of the force is
a small fraction of the vertical component, so the fiber will bend toward
the substrate.
Figure 2: Dimensionless capillary force directions and
relative magnitudes exerted on a perfectly rigid fiber as a function of
fiber position for the system as described by parameters in the top section
of table I.
The maximum dimensionless force magnitude is 0.151. The fiber is assumed
to be aligned parallel to the pad, and height is measured from the fiber
axis to the substrate pad.
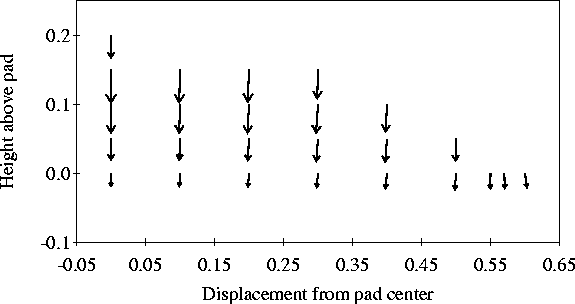 |
When the fiber is allowed to bend, the extent of fiber deflection due
to capillary force (calculated within Surface Evolver as described above)
is significant. For the conditions given in table I,
deflection at the free end reaches a maximum of 0.103, which is more than
half the fiber diameter. Figure 3
shows the solder surface under such conditions.
Figure 3: Three views of the calculated solder surface
shape around a fiber pulled out of alignment by capillary forces. The grey
cylinder shows the original fiber position, and the box is aligned with
the fiber to show the angle of fiber deflection relative to the substrate.
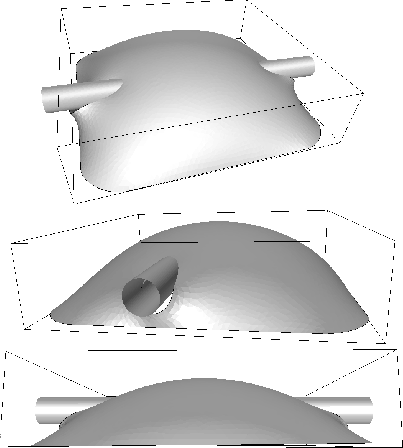 |
For the parameters given here, fiber diameter has the largest effect
on displacement: when the diameter increases from 0.2 to 0.3, the maximum
deflection falls to just 0.0044, which is 1.5% of the diameter. This is
because the elastic energy (equation 1)
is considerably more dependent on the fiber diameter than the surface energy.


Next:Solidification
and coolingUp:MODEL
RESULTSPrevious:MODEL
RESULTS
Adam Clayton Powell IV
1998-06-08